Battery management system (BMS) is technology dedicated to the oversight of a battery pack, which is an assembly of battery cells, electrically organized in a row x column matrix configuration to enable delivery of targeted range of voltage and current for a duration of time against expected load scenarios.
What is a Battery Management System?
BMS is a technology developed to foresee the battery’s State of Charging (SOC) and State of Health (SOH). SOC is the available energy that can be converted to work at that specific time. SOH is a factor that indicates the life cycle and durability of the battery.
When high voltage is required, we cannot rely on a single cell to generate it. Only a series or parallel connection of cells can meet the requirements. Many cells arranged together constitute a module, and several modules and a Battery Management System form a battery pack. For example, a Tesla Model S Plaid battery pack consists of 7,920 lithium-ion cells installed in five modules, and its capacity is 99 kWh.
1. State of Charging (SOC)
An effective BMS system tracks individual batteries’ charging and discharging status and distributes the current accordingly. It ensures that no cell is overcharged or discharged below its lower limit and makes it function within the Safe Operating Area (SOA). It will ensure that the voltage limit is never exceeded.
The BMS would perform some key calculations for estimating the cell’s charge and discharge current limits. It calculates its operating time, energy discharges in the previous cycle and the total number of charging and discharging cycles. With the help of these calculations, it predicts the SOC, which is like a fuel indicator of electric vehicles.
2. State of Health (SOH)
All rechargeable batteries can undergo only a finite number of charging and discharging cycles called cycle life. The cycle life can be optimised by effectively monitoring the charge of the battery while charging and discharging. Under proper circumstances and maintenance, a battery could last a long time.
3. Thermal Management
Thermal management is the most important function carried out by the Battery Management System. It always checks the temperature and cools the battery when needed. Cooling of batteries is not only vital in avoiding thermal runaway but also in optimising efficiency. Thermal management systems are designed considering battery size, peak voltage value, cost, and geographic location. Every battery has a specified operating temperature at which it can work with maximum efficiency. An increase in the battery’s temperature can reduce its efficiency by up to 50%.
A battery pack could use air or liquid coolant to maintain within the permissible temperature range. The efficiency of air coolant is relatively lower than that of liquid coolant. Air coolant systems are often passive and need additional components like an air filter and fan, which increases the system’s weight. Liquid coolant has a higher cooling potential, and batteries are immersed in the liquid.
The Battery Management System controls all these parameters through effective monitoring. It gathers all data related to battery temperature, the flow of current in and out of the cell, the flow of coolant, speed of vehicle and state of power. Whenever the battery gets heated, it signals the pumping unit to deliver more coolant. In the same way, whenever the voltage requirement is increased, it sends requests to lower the current limits. Thus the battery management system helps to ensure the safety and life of the battery.
What is the Function of a Battery Management System?
The primary function of the BMS is to protect the battery cells from damage caused by being overcharged or over-discharged. Additionally, the BMS calculates the remaining charge, monitors the battery’s temperature, monitors the battery’s health and safety by checking for loose connections and internal shorts. The BMS also balances the charge across the cells to keep each cell functioning at maximum capacity.
If it detects any unsafe conditions, the BMS shuts the battery down to protect the lithium-ion cells and the user.
Why are battery management systems (BMS) needed and how do they work?
Battery management systems (BMS) are electronic control circuits that monitor and regulate the charging and discharge of batteries. The battery characteristics to be monitored include the detection of battery type, voltages, temperature, capacity, state of charge, power consumption, remaining operating time, charging cycles, and some more characteristics.
Why a BMS is Important
Battery management systems are critical in protecting the battery’s health and longevity but even more important from a safety perspective. The liquid electrolyte in lithium-ion batteries is highly flammable.
So, these batteries need to be operating optimally and within safety limits at all times to prevent a fire.
Protections Offered By a Battery Management System
Let’s review the protections of a battery management system:
Under and Over-Voltage
Damage occurs if you overcharge (cell voltage getting too high) or over-discharge (cell voltage gets too low) a lithium-ion battery cell. The BMS helps protect from under and over-voltage situations so that damage to the battery’s cells does not occur.
Temperature Extremes
The safety and stability of lithium-ion battery cells depend on temperature maintenance within certain limits. If the temperature exceeds the critical level on either end, thermal runaway can occur. Consequently, this can lead to an inextinguishable fire.
The BMS monitors the temperature and sometimes controls cooling fans (in the case of an electric vehicle) to help maintain proper conditions. It will even shut down cells if needed to protect the battery.
Protection from Shorts
Internal and external shorts can also lead to thermal runaway. For this reason, protection from shorts is another critical component of a battery management system.
Types of battery management systems
Battery management systems range from simple to complex and can embrace a wide range of different technologies to achieve their prime directive to “take care of the battery.” However, these systems can be categorized based upon their topology, which relates to how they are installed and operate upon the cells or modules across the battery pack.
Centralized BMS Architecture
Has one central BMS in the battery pack assembly. All the battery packages are connected to the central BMS directly. The structure of a centralized BMS is shown in Figure 6. The centralized BMS has some advantages. It is more compact, and it tends to be the most economical since there is only one BMS. However, there are disadvantages of a centralized BMS. Since all the batteries are connected to the BMS directly, the BMS needs a lot of ports to connect with all the battery packages. This translates to lots of wires, cabling, connectors, etc. in large battery packs, which complicates both troubleshooting and maintenance.
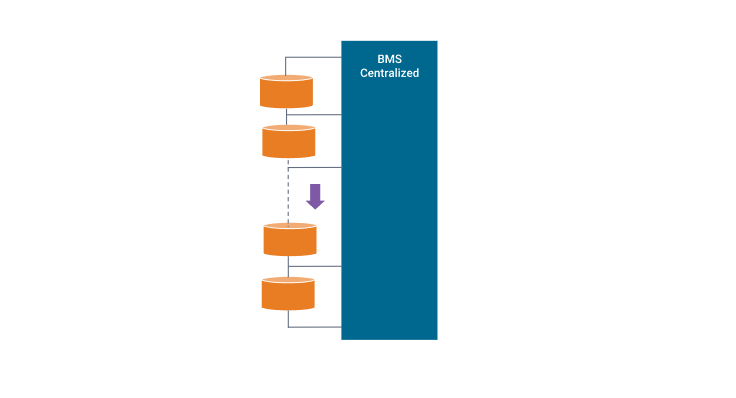
Modular BMS Topology
Similar to a centralized implementation, the BMS is divided into several duplicated modules, each with a dedicated bundle of wires and connections to an adjacent assigned portion of a battery stack. See Figure 7. In some cases, these BMS submodules may reside under a primary BMS module oversight whose function is to monitor the status of the submodules and communicate with peripheral equipment. Thanks to the duplicated modularity, troubleshooting and maintenance is easier, and extension to larger battery packs is straightforward. The downside is overall costs are slightly higher, and there may be duplicated unused functionality depending on the application.
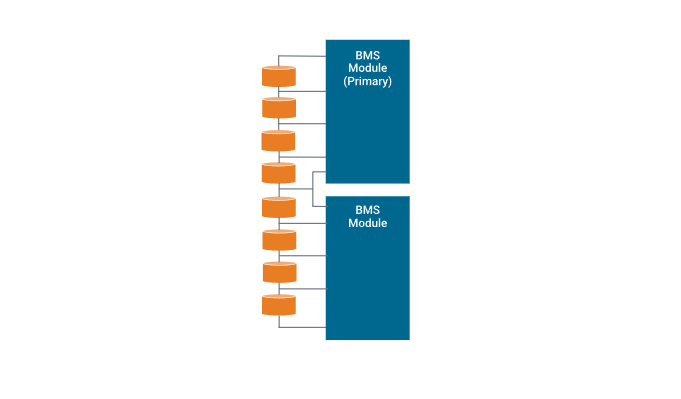
Primary/Subordinate BMS
Conceptually similar to the modular topology, however, in this case, the slaves are more restricted to just relaying measurement information, and the master is dedicated to computation and control, as well as external communication. So, while like the modular types, the costs may be lower since the functionality of the slaves tends to be simpler, with likely less overhead and fewer unused features.
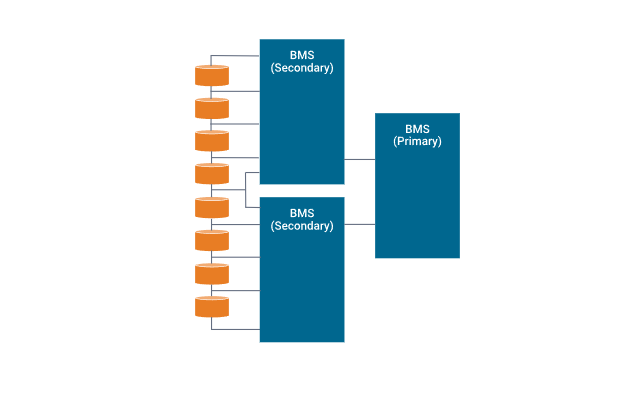
Distributed BMS Architecture
Considerably different from the other topologies, where the electronic hardware and software are encapsulated in modules that interface to the cells via bundles of attached wiring. A distributed BMS incorporates all the electronic hardware on a control board placed directly on the cell or module that is being monitored. This alleviates the bulk of the cabling to a few sensor wires and communication wires between adjacent BMS modules. Consequently, each BMS is more self-contained, and handles computations and communications as required. However, despite this apparent simplicity, this integrated form does make troubleshooting and maintenance potentially problematic, as it resides deep inside a shield module assembly. Costs also tend to be higher as there are more BMSs in the overall battery pack structure.
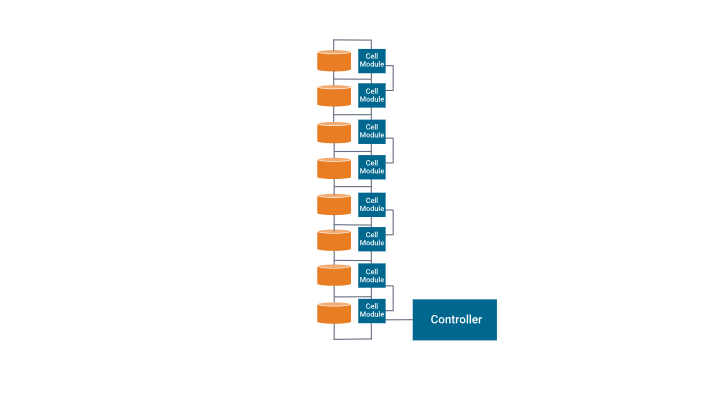
The benefits of battery management systems
An entire battery energy storage system, often referred to as BESS, could be made up of tens, hundreds, or even thousands of lithium-ion cells strategically packed together, depending on the application. These systems may have a voltage rating of less than 100V, but could be as high as 800V, with pack supply currents ranging as high as 300A or more. Any mismanagement of a high voltage pack could trigger a life-threatening, catastrophic disaster. Consequently, therefore BMSs are absolutely critical to ensure safe operation. The benefits of BMSs can be summarized as follows.
Functional Safety. Hands down, for large format lithium-ion battery packs, this is particularly prudent and essential. But even smaller formats used in, say, laptops, have been known to catch fire and cause enormous damage. Personal safety of users of products that incorporate lithium-ion powered systems leaves little room for battery management error.
Life Span and Reliability. Battery pack protection management, electrical and thermal, ensures that all the cells are all used within declared SOA requirements. This delicate oversight ensures the cells are taken care of against aggressive usage and fast charging and discharging cycling, and inevitably results in a stable system that will potentially provide many years of reliable service.
Performance and Range. BMS battery pack capacity management, where cell-to-cell balancing is employed to equalize the SOC of adjacent cells across the pack assembly, allows optimum battery capacity to be realized. Without this BMS feature to account for variations in self-discharge, charge/discharge cycling, temperature effects, and general aging, a battery pack could eventually render itself useless.
Diagnostics, Data Collection, and External Communication. Oversight tasks include continuous monitoring of all battery cells, where data logging can be used by itself for diagnostics, but is often purposed to the task for computation to estimate the SOC of all cells in the assembly. This information is leveraged for balancing algorithms, but collectively can be relayed to external devices and displays to indicate the resident energy available, estimate expected range or range/lifetime based on current usage, and provide the state of health of the battery pack.
Cost and Warranty Reduction. The introduction of a BMS into a BESS adds costs, and battery packs are expensive and potentially hazardous. The more complicated the system, the higher the safety requirements, resulting in the need for more BMS oversight presence. But the protection and preventive maintenance of a BMS regarding functional safety, lifespan and reliability, performance and range, diagnostics, etc. guarantees that it will drive down overall costs, including those related to the warranty.
Tasks of smart battery management systems (BMS)
The task of battery management systems is to ensure the optimal use of the residual energy present in a battery. In order to avoid loading the batteries, BMS systems protect the batteries from deep discharge and over-voltage, which are results of extreme fast charge and extreme high discharge current. In the case of multi-cell batteries, the battery management system also provides a cell balancing function, to manage that different battery cells have the same charging and discharging requirements.
Frequently Asked Questions
What are the different types of battery management systems?
There are two main types of BMSs. The first is a centralized BMS, which uses one control unit to manage all of the battery cells in the system. The second type of BMS is a distributed BMS, which uses multiple control units to manage the battery cells in the system.
Do all LiFePO4 batteries have BMS?
BMS, Battery Management System, is a mandatory component for LiFePO4 batteries.
What is the maximum voltage for LiFePO4 BMS?
In the case of LiFePO4 chemistry, the absolute maximum is 4.2V per cell, though it is recommended that you charge to 3.5-3.6V per cell, there is less than 1% extra capacity between 3.5V and 4.2V. Over charging causes heating within a cell and prolonged or extreme overcharging has the potential to cause a fire.
What is the role of BMS in battery charging?
The task of battery management systems is to ensure the optimal use of the residual energy present in a battery. In order to avoid loading the batteries, BMS systems protect the batteries from deep discharge and over-voltage, which are results of extreme fast charge and extreme high discharge current.
Does my battery need a BMS?
Battery Management Systems (BMSs) are crucial for the safe and reliable operation of battery energy storage systems. One of the most significant benefits of a BMS is that it ensures functional safety, particularly for large-format lithium-ion battery packs.
How does BMS protect battery?
A BMS may protect its battery by preventing it from operating outside its safe operating area, such as: Over-charging. Over-discharging. Over-current during charging.
Does BMS limit voltage?
This value is the maximum cell voltage that the BMS is using to limit how high individual cell voltages can be. This can be useful for communicating with chargers or charging stations expecting a maximum cell voltage value that they are able to charge up to.